IMG - Injection Molding Guide
“Your path to a fully standardized, digital and networked “red thread” through the mould sampling process and beyond to the running series productions…”
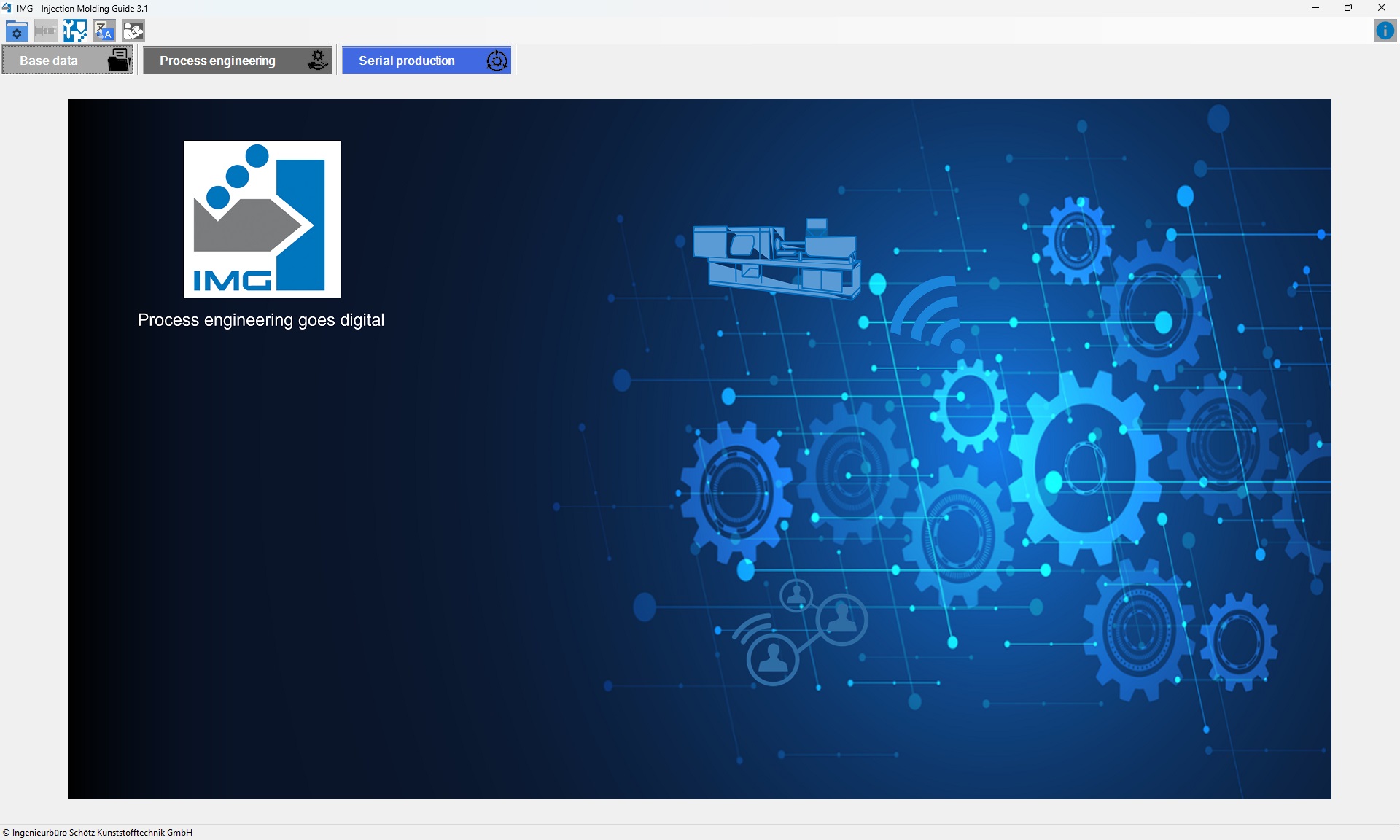
The IMG enables a process-oriented and user-friendly standardized, digitized and at the same time networked platform in the company that can be used by all departments, such as project managers, developers, designers, quality assurance, toolmaking and production. As a workflow-supported control system (“toolbox”), the platform also offers a digital transformation of your entire process engineering and subsequent series process.

Contact us for a non-binding needs assessment!
Make an appointment now, it's fast and easy at info@kunststofftechnik-ingenieurbuero.de or 09128/9071393.
The IMG can be subsidized by the state: digital funding programs
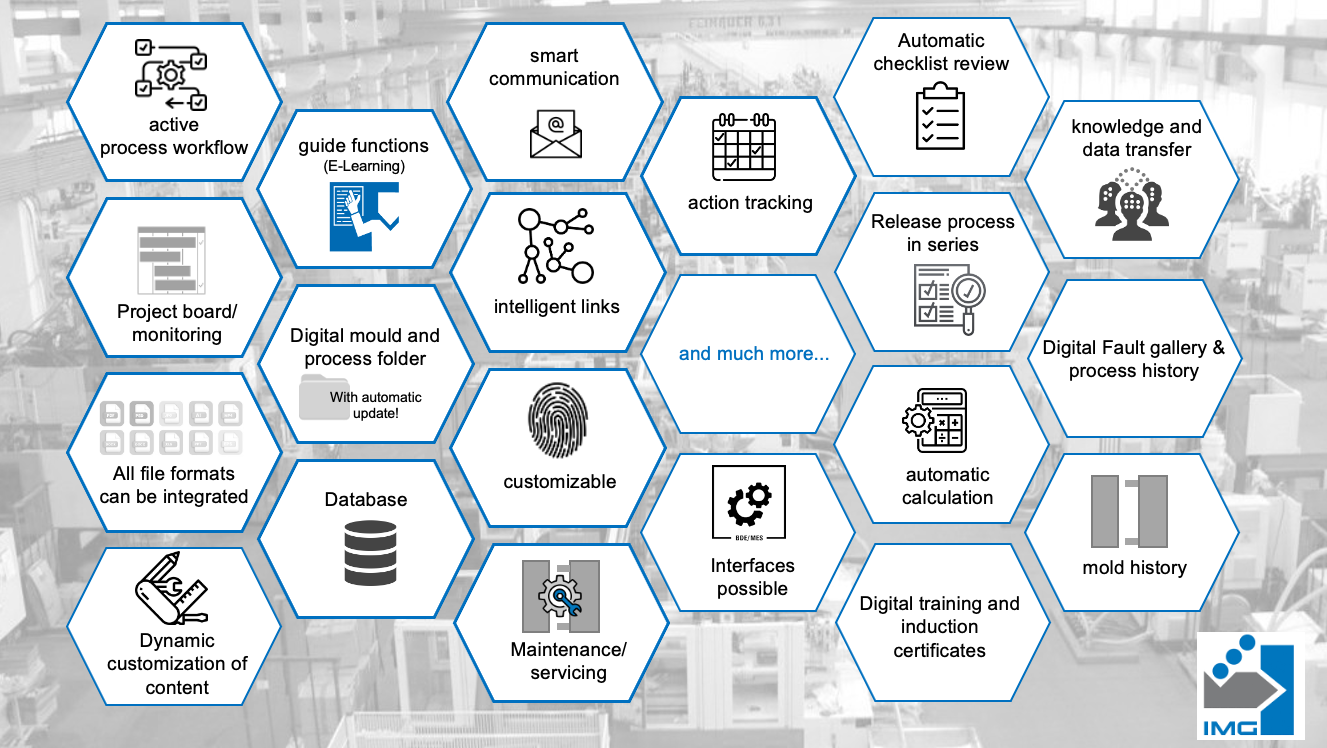
Simplify you data exchange nationally or worldwide...!
The master data can be used to save time in advance.
The IMG offers the following advantages:
- Data can be stored fast and easily and is used by the individual departments throughout the entire sampling and subsequent series production process as a means of transferring information and data.
- With the help of the internal database, all the data created, such as the plastic to be processed or the injection molding machine used, can be stored.
- Documents, templates, images and photos can be integrated and edited.
- Numerous links from the master data later contribute to a more effective and time-saving processing of the individual steps in the software.
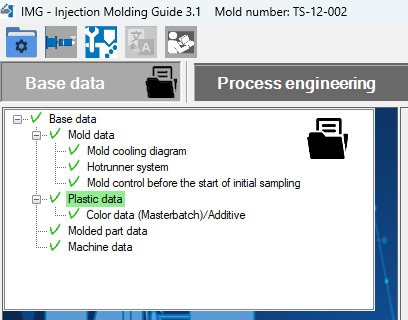
Standardize and digitize your process nationally or worldwide...!
Operational implementation
with the IMG
Once all the important background information has been prepared, entered and saved under master data, the operational part on the machine can begin.
The user can select from the following categories using the “Add new sample” button (Fig. 1),
such as:
- Initial sampling of the injection mold
- further follow-up sampling
- process optimization
- material sample
- complaint
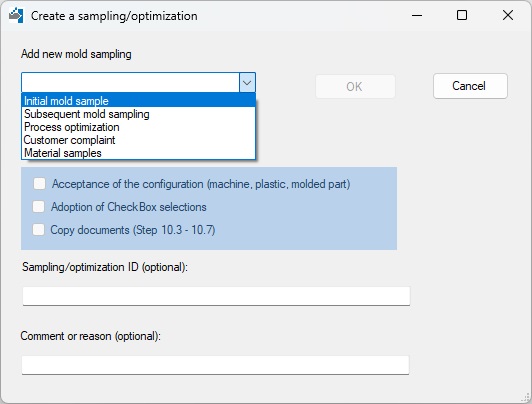
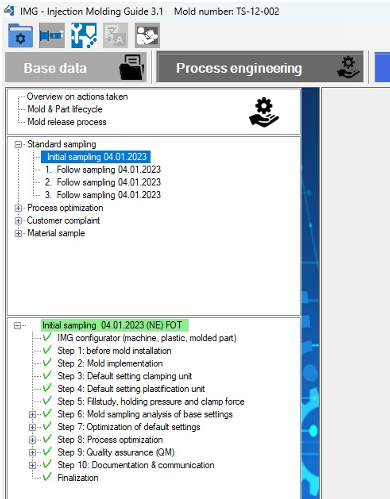
Use IMG to network internally, nationally or worldwide...!
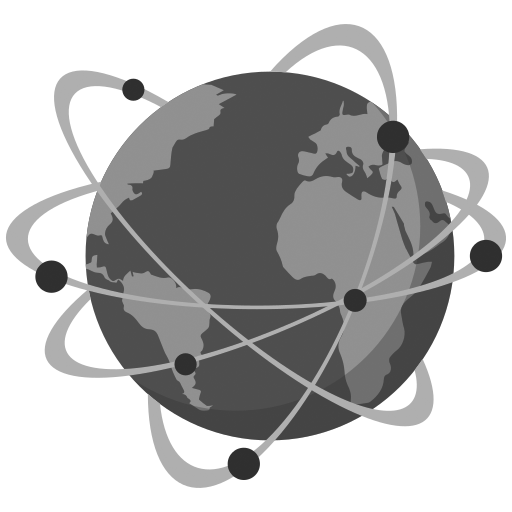
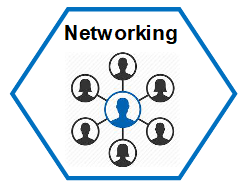
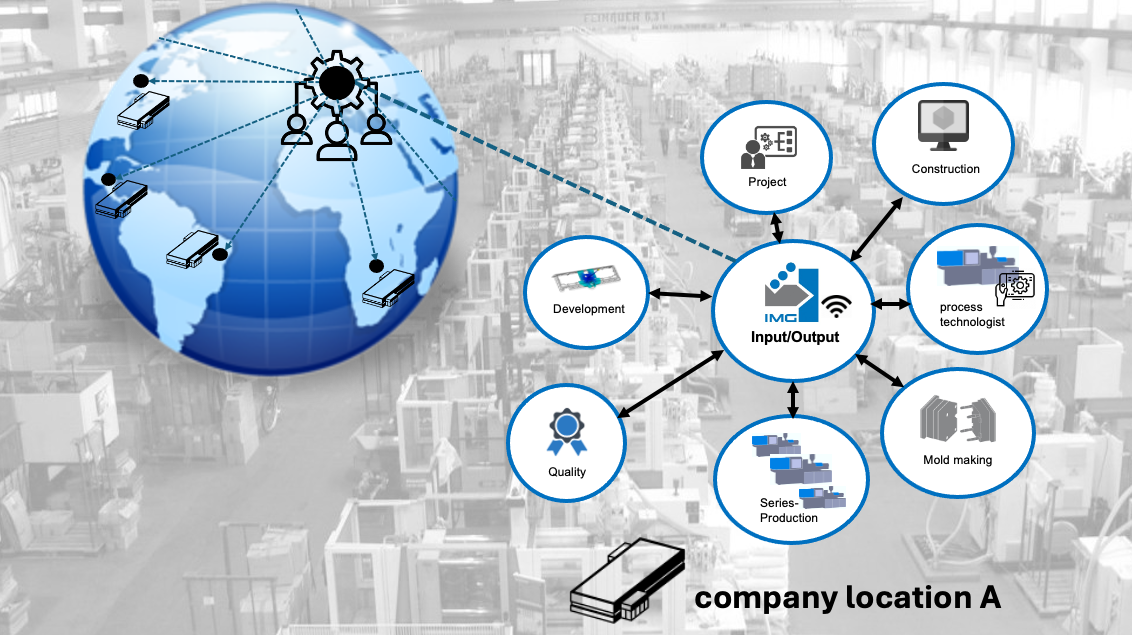
Many companies have other plants in addition to their headquarters, both nationally and globally, all over the world.
Use IMG software here too to implement your standardized process nationally or globally, to build injection molding processes together, to inspect them or to provide support when problems arise.
IMG-training offensive national or worldwide...!
If the user needs more background information during the running of the sample or process optimization, for example for the setting strategy of the basic setting of machine settings and process parameters, the integrated guide with numerous instructions, graphics, tables, photos/images, leads the user through all the sample or optimization steps on the machine.
IMG-Series production
The process engineering and its challenges in everyday life do not end with the sampling process. Take advantage of all the benefits of IMG throughout your entire production life cycle.
Digital process folder:
- No more paper at the machine
- Automatic update after each release process
- Securing the master setting (data record) & all relevant production documents
- High process reliability and fast data transfer at the machine
error catalog with gallery
- creation of your own individual error database
- fast query in the running series process using intelligent search functions
process history
- employee-led approach to faults in the running series process with guided “IMG process check”
- simple and intuitive user interfaces
- fast information transfer to employees responsible for the process
and much more...
IMG-architecture
Function: Client/Server Implementation
The client/server model (also known as the client/server concept, architecture, system or principle) describes the possibility of distributing all IMG contents within a network. The IMG software is divided into the IMG frontend (clients) and the IMG backend (server).
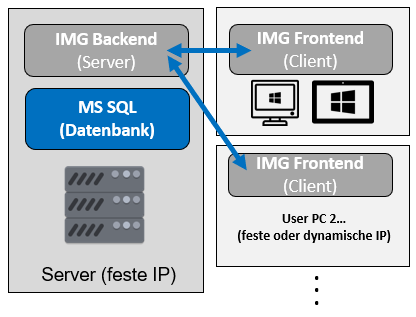
Benefit through the IMG...
Standardized workflow complete and ready for use...
- Problem, time and cost reduction of the entire process
- Reduction of throughput times until series production
- Saving of costs and resources
- Faster implementation of an individual mould sampling
- Improvement of communication and documentation among the specialist departments
- Improvement of productivity, profitability and energy efficiency of each injection moulding process
- Clear, transparent and structured process internally, nationally and globally
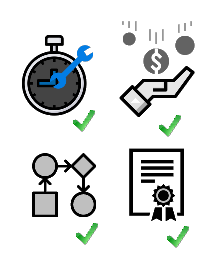
Digitized & networked process
- Faster exchange of information and data transfer possible before, during and after the mould sampling
- Parallel work on the project by all departments involved before, during and after the mould sampling saves resources, time and money
- Intelligent document management
- Mobile with tablet, laptop to implement the sampling process at external suppliers
(e.g. the first mould commissioning at the toolmaker in China)
- No data islands in individual departments
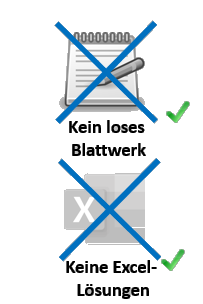
Test it out with no cost and no obligation...!
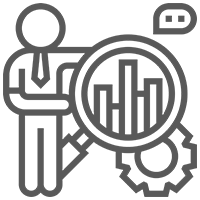
How? It's easy.
Step 1: Get in touch with us...
info(at)kunststofftechnik-ingenieurbuero.de
IMG-Hotline: +49 (0)9128 9071393
Step 2: Kick-off
- When would you like to test?
- How many test licenses do you need to show an optimal workflow in your company?
- Who is your responsible IT employee (contact person)?
Step 3: Contacting internal IT
- Contact details of the IT employee
- Our IT department will exchange information with your IT department and clarify all details
- Scheduling (start of test phase)
Step 4: Installation of test licenses
- Our IT will support you with this
- Activation of the test licenses from the start of the test phase (21 days, optionally also extendable)
Step 5: Start of the test phase
- Technical support via TelKo, WebEX or TeamViewer during the test phase as required.
And off we go...